This is my build log for the
MIDI Player motor build I have
made.
Here is a shot of the motor after
removing it from its mounting
plate in the player:
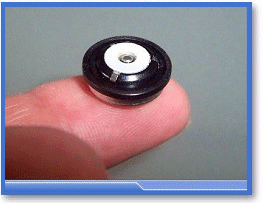
I managed to almost buckle the
shaft mount of the Can while banging
out the rotor shaft as I wasn't
sure how they got it in there.
Lesson learnt, remove the little
backing plate from the rear and
take off the copper clip holding
the shaft in place.
I punched out the centre brass
sleeve from the stator and wound
it up with 15 turns of 30 gauge:
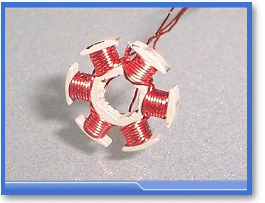
Removing the Rotor revealed what
I thought was a plastic face with
a flux ring mounted in it. Cutting
away the plastic revealed that
there was a whole metal Rotor
there but it had been pancaked
both sides in plastic - so I cut
it all away - straightened the
shaft mount and polished it up.
A bonus was all those 'cooling
holes' were already there to keep
both plastic sides together!
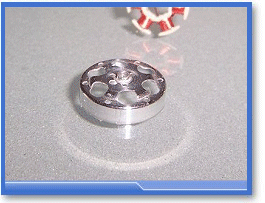
Next I mounted 8 3x3x0.5mm magnets
I had purchased from olmodfrom
RCGroups a while ago - I knew
they would come in handy one day.
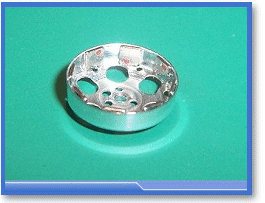
I went to another LHS yesterday
and found some metric tubing perfect
for the job - so still no lathe
work done. 4mmODx3mmID aluminium
tubing for the stator mount and
1.5mmODx1mmID brass shaft sleeve.
AUW so far is 1.7 grams.
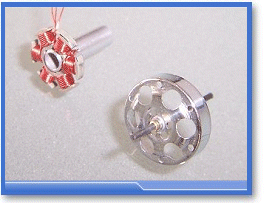
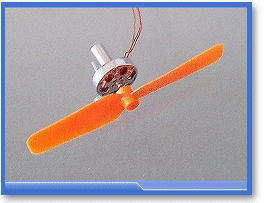
The bearings arrived this morning
so I wasted no time installing
them into the stator shaft. I
almost thought they were too small
when I saw them as I have only
seen the flanged type.
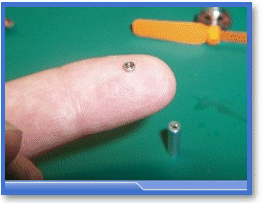
I hooked up the finished motor
to a CC 10A esc and 2 cell 340mah
kokam. The motor absolutely screamed
at up to half throttle with the
2.5" gws prop and even faster
with the cut down prop - I didnt
dare throttle up any higher! It
got hot, which is to be I expected
as I have wound this for a one
cell 90mah cell. Now that I know
it runs great, next I will test
it on the BLC-1 esc and 90mah
cell and see how it performs.
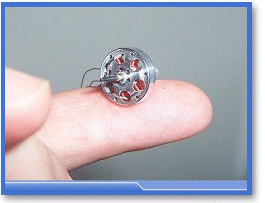
AUW for finished motor
is 1.78 grams!!!
So far I have had to increase
the winds to 28 turns as 15 turns
was just too dang hot! The motor
runs cold but I can't run it WOT
as the blc gets too hot. And that
was testing on a 210mah lipo.
I tested it on a 145mah lipo and
it couldn't deliver top end current
at WOT, so I am still too hot
for the battery and ESC. I may
have to step down in wire size
and throw a bunch more turns on
it as it has sufficient revs at
half to 2/3rd throttle for my
needs. Full throttle was just
crazy. So I think I will try for
~50 turns of 30gauge and see how
that goes next. AUW with extra
turns put it at 2.0 grams. This
shouldn't move too much with the
new wind. I think for now I will
run 160 mah lipos as I have a
bunch of them that have yet to
be used.
Final progress is I tried 36
winds of a paired 30 gauge wind
and it was still drawing too much
current for the esc. The motor
ran fairly warm. I wound 36 turns
of the orginal gauge and that
was a real tight fit. I had to
squash the coils down to get the
Bell back on! It still runs the
ESC hot at WOT and the motor was
stone cold with these windings.
My only conclusion is the airgap
is requiring a decent amount of
current to get things going.